WELDING DEFECTS APPEARS IN RADIOGRAPHY TEST
- MNH Askary
- Oct 19, 2017
- 3 min read
Classification of weld cracks
How to identify Transverse Crack or Longitudinal Crack?

Porosity (PO)
Porosity is the result of gas entrapment in the solidifying metal. Porosity can take many shapes on a radiograph but often appears as dark round or irregular spots or specks appearing singularly, in clusters or rows. Sometimes porosity is elongated and may have the appearance of having a tail This is the result of gas attempting to escape while the metal is still in a liquid state and is called wormhole porosity. All porosity is a void in the material it will have a radiographic density more than the surrounding area.

Cluster porosity
Cluster porosity is caused when flux coated electrodes are contaminated with moisture. The moisture turns into gases when heated and becomes trapped in the weld during the welding process. Cluster porosity appears just like regular porosity in the radiograph but the indications will be grouped close together.

Slag inclusion (SI)
Slag inclusions are nonmetallic solid material entrapped in weld metal or between weld and base metal. In a radiograph, dark, jagged asymmetrical shapes within the weld or along the weld joint areas are indicative of slag inclusions.

Incomplete penetration (IP)
Incomplete penetration (IP) or lack of penetration (LOP) occurs when the weld metal fails to penetrate the joint. It is one of the most objectionable weld discontinuities. Lack of penetration allows a natural stress riser from which a crack may propagate. The appearance on a radiograph is a dark area with well-defined, straight edges that follow the land or root face down the centre of the weldment.
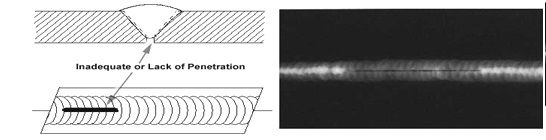
Incomplete fusion (LF)
Incomplete fusion or lack of fusion is a condition where the weld filler metal does not properly fuse with the base metal. Appearance on radiograph: usually appears as a dark line or lines oriented in the direction of the weld seam along the weld preparation or joining area.
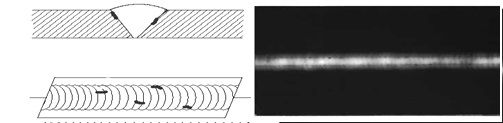
Internal concavity
Internal concavity or suck back is a condition where the weld metal has contracted as it cools and has been drawn up into the root of the weld. On a radiograph, it looks similar to lack of penetration but the line has irregular edges and it is often quite wide in the centre of the weld image.
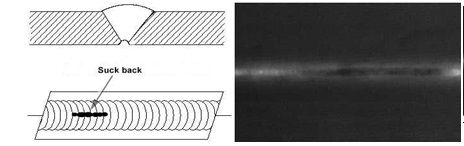
Root Undercut
Internal or root undercut is an erosion of the base metal next to the root of the weld. In the radiographic image, it appears as a dark irregular line offset from the centerline of the weldment. Undercutting is not as straight-edged as LOP because it does not follow a ground edge.

External Undercut
External or crown undercut is an erosion of the base metal next to the crown of the weld. In the radiograph, it appears as a dark irregular line along the outside edge of the weld area.
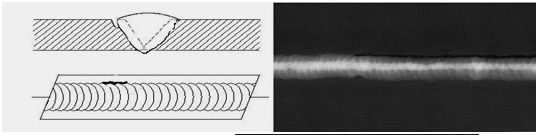
Mismatch
Offset or mismatch are terms associated with a condition where two pieces being welded together are not properly aligned. The radiographic image is a noticeable difference in density between the two pieces. The difference in density is caused by the difference in material thickness. The dark, straight line is caused by the failure of the weld metal to fuse with the land area.

Inadequate weld reinforcement
Inadequate weld reinforcement is an area of a weld where the thickness of weld metal deposited is less than the thickness of the base material. It is very easy to determine by radiograph if the weld has inadequate reinforcement because the image density in the area of suspected inadequacy will be more (darker) than the image density of the surrounding base material.

Excess weld reinforcement
Excess weld reinforcement is an area of a weld that has weld metal added in excess of that specified by engineering drawings and codes. The appearance on a radiograph is a localized, lighter area in the weld. A visual inspection will easily determine if the weld reinforcement is in excess of that specified by the engineering requirements.
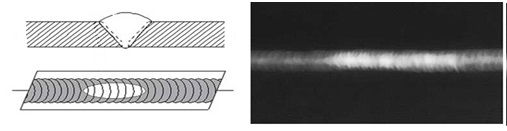
Crack
Cracks can be detected in a radiograph only when they are propagating in a direction that produces a change in thickness that is parallel to the x-ray beam. Cracks will appear as jagged and often very faint irregular lines. Cracks can sometimes appear as "tails" on inclusions or porosity.
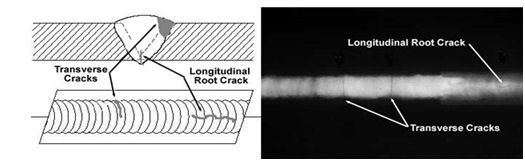
Comentarios